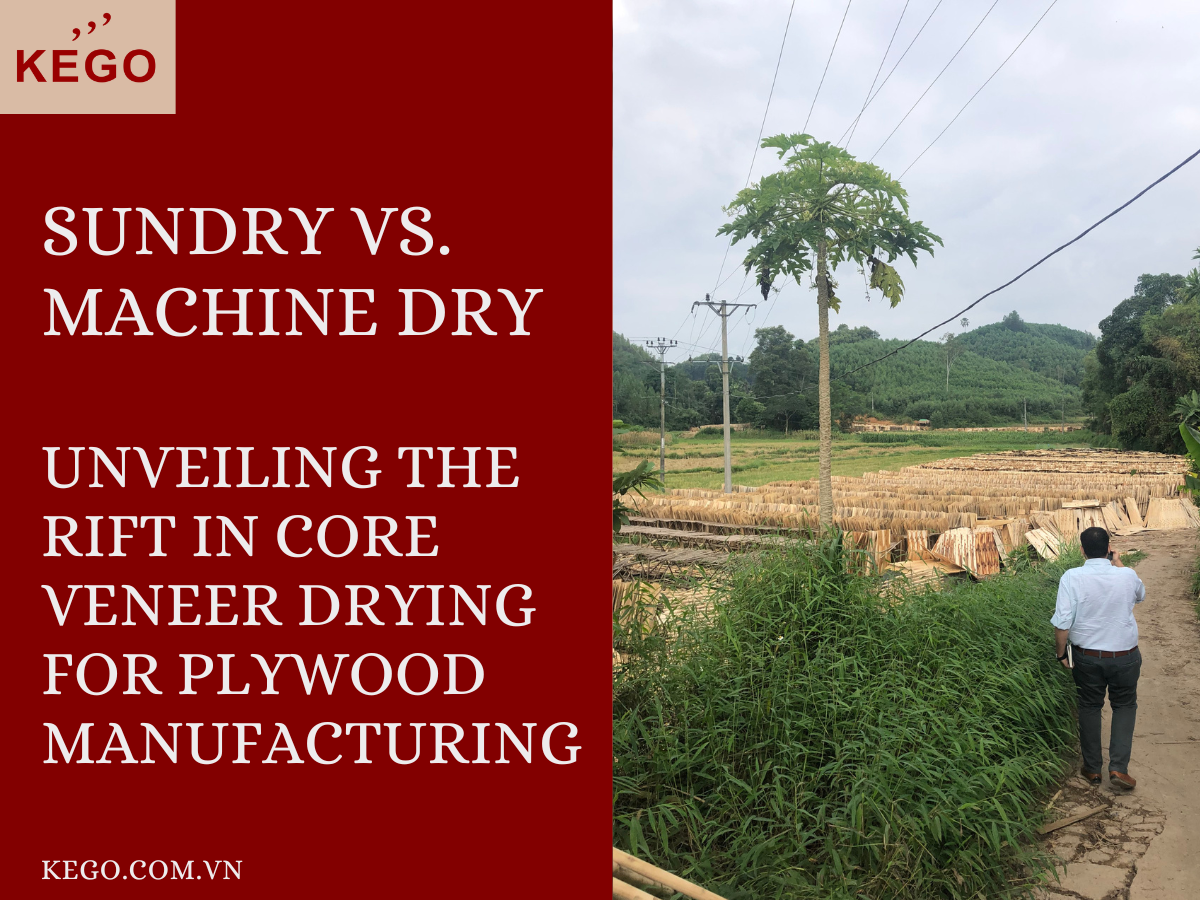
Introduction
In the intricate world of plywood manufacturing, the process of drying core veneers plays a pivotal role in determining the quality and performance of the final product. Two primary methods, sundry drying, and machine drying, have emerged as contenders in the pursuit of achieving optimal veneer moisture content. Let’s delve into the nuances that set sundry and machine dry apart, unraveling their impact on plywood production.
Understanding Sundry Drying
Sundry drying is a traditional method that relies on the natural elements of air and sunlight to reduce the moisture content of core veneers. This age-old technique involves stacking veneers in open-air yards, allowing them to be exposed to the sun and wind. Sundry drying, while inherently reliant on weather conditions, offers some distinct advantages.
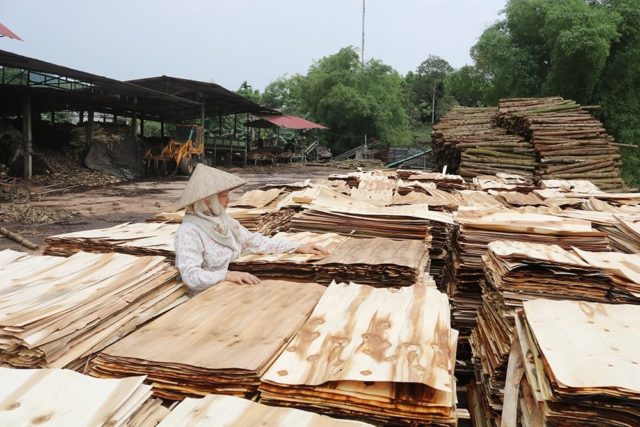
Pros of Sundry Drying
- Cost-Effectiveness: Sundry drying requires minimal infrastructure, making it a cost-effective option for plywood manufacturers, especially in regions with abundant sunlight.
- Natural Characteristics: Veneers dried through sundry methods often retain their natural color and texture, contributing to a more authentic appearance in the final plywood product.
Challenges with Sundry Drying
- Weather Dependency: The effectiveness of sundry drying is heavily contingent on weather conditions. Excessive rain or prolonged cloudy periods can significantly hinder the drying process.
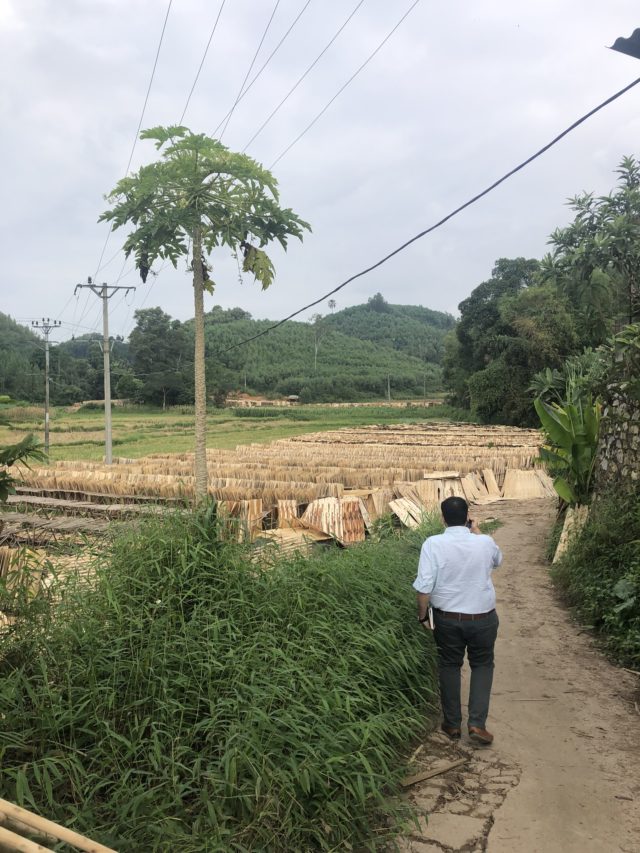
2. Time-Consuming: Sundry drying tends to be a time-consuming method, extending the overall production timeline.
The Rise of Machine Drying

In contrast to sundry drying, machine drying introduces a controlled and mechanized approach to reducing veneer moisture content. Plywood manufacturers have increasingly embraced this method for its efficiency, consistency, and reduced dependency on external factors.
Pros of Machine Drying
- Precision and Control: Machine drying allows for precise control over temperature, humidity, and drying duration, ensuring uniform moisture removal from each veneer.
Kego dry machine2. Time Efficiency: Compared to sundry drying, machine drying significantly reduces the overall drying time, streamlining the production process.
Challenges with Machine Drying
- Capital Investment: Implementing machine drying requires a significant upfront investment in specialized equipment, which may pose a barrier for some manufacturers.
- Potential Quality Impact: While machine drying provides efficiency, some argue that it may alter the natural characteristics of veneers, potentially affecting the final aesthetic of the plywood.
Conclusion
The choice between sundry and machine drying in plywood manufacturing hinges on various factors, including geographic location, budget constraints, and desired product characteristics. Both methods have their merits and drawbacks, and manufacturers must carefully evaluate their priorities to select the drying method that aligns with their specific needs and goals. As technology advances, the plywood industry continues to evolve, and innovations may bridge the gaps between these two distinct approaches, leading to hybrid methods that combine the best of both worlds.
Contact Kego Co., Ltd
Experience the difference of premium timber exports with Vietnam Plywood. Explore our product range, learn more about our sustainable practices, and contact us for personalized assistance. Trust us to be your reliable partner in quality plywood exports.
Call us:+ 8424 3222 2333 – +84 97 999 5346 (Whatsapp)
Email us:sales@kego.com.vn
Location:R.603 Kim Anh Building, Lane 78, Duy Tan Street, Cau Giay District, Hanoi.