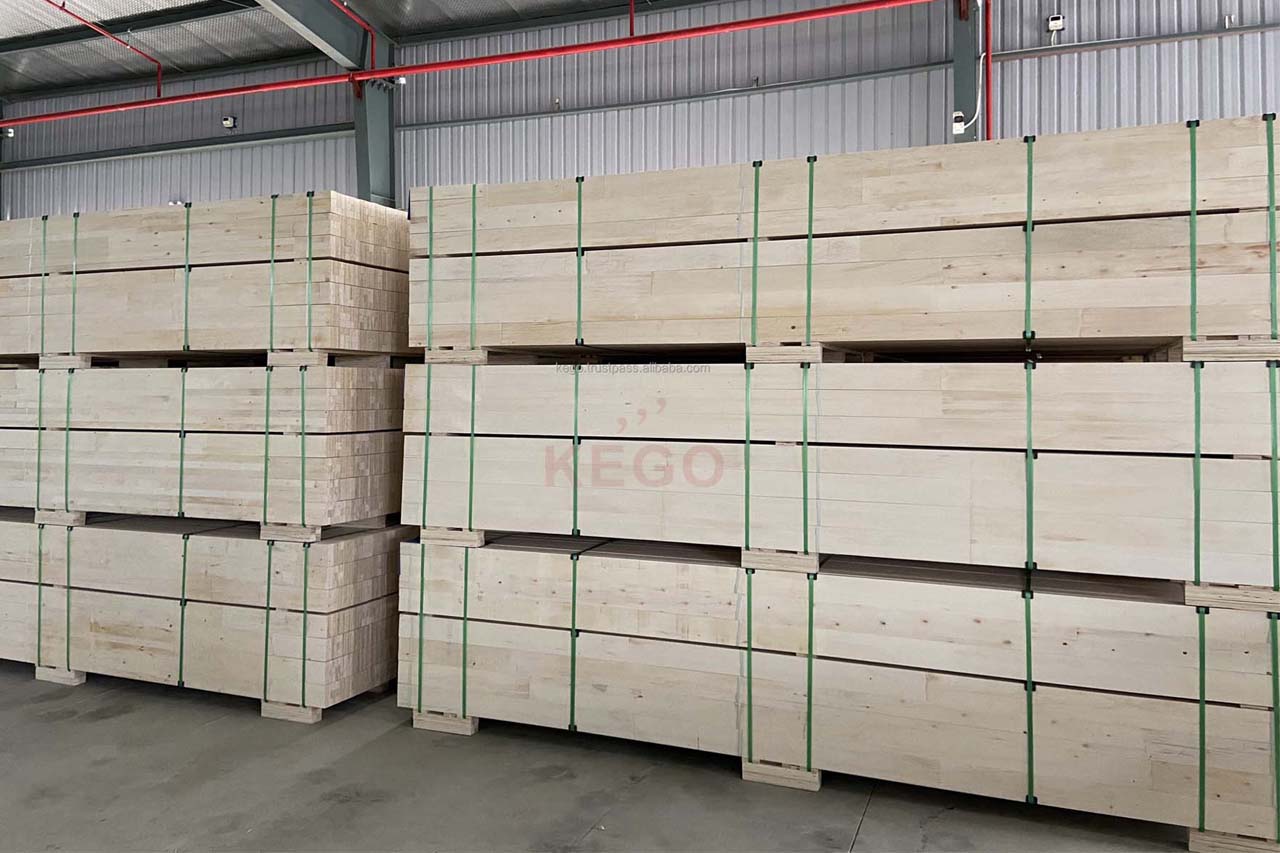
Laminated veneer lumber (LVL) is a composite product manufactured from multiple thin layers of veneer that are aligned with the length of the finished lumber. LVL can be manufactured to almost any size and provides a cost-effective and sustainable structural reliability and strength. That’s why LVL is the most preferable and become more and more popular in our daily life, especially in packaging and construction area.
The similarity between Packaging LVL and Construction LVL
Production process:
Not only packaging LVL but also construction one has the same production process. There are 10 steps to produce laminated veneer lumber:
STEP 1: Cut the log to size.
STEP 2: Peeling the Log to the veneer. In this step of LVL Production, peels large log pieces into thin veneer sheets using the rotary peeling technique.
STEP 3: Drying the Veneer. It is very important to the veneers sheets before going to the next process. The thickness of veneers decreases after this process but it is very less.
STEP 4: Grading the Veneer. A, B, C.
STEP 5: Gluing the veneer.
STEP 6: Laying the veneer. In typical manufacture, all veneers are laid up so the grain direction is the same in all veneers.
STEP 7: Hot pressure. After the adhesive process, high heat and pressure are applied. So that all the Layers stick well to each other with Adhesive and make a strong structure. Which lasts for a long time.
STEP 8: Sanding the core (Optional) This step will help the LVL have smooth face in acceptable tolerance of thickness.
STEP 9: Cutting to size.
STEP 10: Packaging.
Material:
Vietnam laminated veneer lumber can be produced from various veneer materials poplar, pine , eucalyptus, rubber, … especially acacia and mixed wood which is popularly grown in Vietnam. Acacia wood is famous for its natural strength, heaviness and durableness. It can be used for any commercial purposes like furniture, packaging, construction and many more.
High strength and good bonding:
Due to the structure of many layers of wood arranged in the same direction, LVL has high strength and great bending strength, easy to bend when needed. Because of that feature, LVL plywood is often used for frame, beams, boards and packing (especially pallet) materials.
The difference:
Glue and usage:
The glues classified into E0, E1 or E2 glue all come from the classification of residual Formalin content in the product, or in other words, the content of free Formalin that exists in the glue is the criterion for classifying the glue which is E0. , E1 or E2.
For packaging LVL, glue E2 is mostly used in production process, which emit more than 0.124 mg/m3 air. Glue E2 can not resist from water so it normally used to produce LVL pallet, LVL sofa frame,…
Other than glue E0, E1, E2, we have WBP glue that is used for Construction LVL. WBP stands for Water Boiling Proof, If you use WBP (phenol) glue for Construction LVL, the panel will can be exposed to weather, water and moisture for a long period without delamination.
Dimension:
Packaging LVL can accept short length, normally below 2440mm, the shortest size can be LVL block which has 3 same dimension, such as 80x80x80 or 90x90x90. This LVL block is used for pallet footer.
Different from Packaging LVL, the length from 3000mm to 5000mm is very popular in construction LVL material, it plays a role as timber beams or lumber purlin.
To sum up, although the quality is still inferior to natural wood, LVL plywood also possesses some outstanding characteristics thanks to controlled specifications. Typically, the structure is firm and hard, it makes Construction LVL and Packaging LVL become more and more popular in our daily life. With competitive price and stable quality, LVL will soon become the mainstay of plywood industry in Vietnam.
Whatever for packaging or construction, Laminated Veneer Lumber need to maintain the strong core and flexible strength, understanding the right requirement, Kego Company Limited would like to introduce to you the suitable choice for your uses as below: